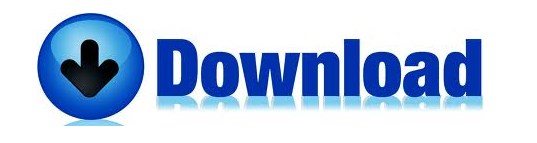
183-192, 2009.] and an existent cohesive zone model proposed by MOURA et al. da Costa Mattos & Marcílio Alves (Editors), Mechanics of Solids in Brazil 2009, pp. 5 5 DE BARROS, S., CHAMPANEY “Crack propagation tests: analytical and numerical approaches” In: H.S. 396-406, 2013.Ĥ DE BARROS, S., CHAMPANEY, L., VALOROSO, N., “Numerical simulations of crack propagation tests in adhesive bonded joints”, Latin American Journal of Solids and Structures. ], and improved by BARROS and CHAMPANEY [ 3 3 DE BARROS, S., CHAMPANEY, L., “Crack Propagation Curves on Flexure Adhesion Tests”, Int.l Journal of Structural Integrity. “Damage Analysis of Interlaminar Fracture Specimens”, Composites Structures, (95)00002-X, v. [ 2 2 ALLIX, O., LADEVÉZE, P., CORIGLIANO, A. So, to bypass the limitation of the other models that needs the crack length measurement during the test, in this work it is proposed the use two different approaches that don’t need the measurement of crack length during tests: a proposed analytical model based on the originally proposed damage model by ALLIX et al. In this work the equation (2) will be used, with solid mechanics beam theory, to assess the fracture toughness of structural adhesive joints in mode II, 𝒢 IIC. This fact is quite restrictive once it is remarkably difficult to access the crack length during its stable growth. Unfortunately, most of these models needs the crack length measurement during the test. There are many models that use equation (2) to access the fracture toughness of an adhesive joint. Where B is the width, P is the loading, C = δ / P is the compliance and a is the crack length. The negative signal of this equation stands for the energy stored in the cracked part decreases as the crack increases its length.
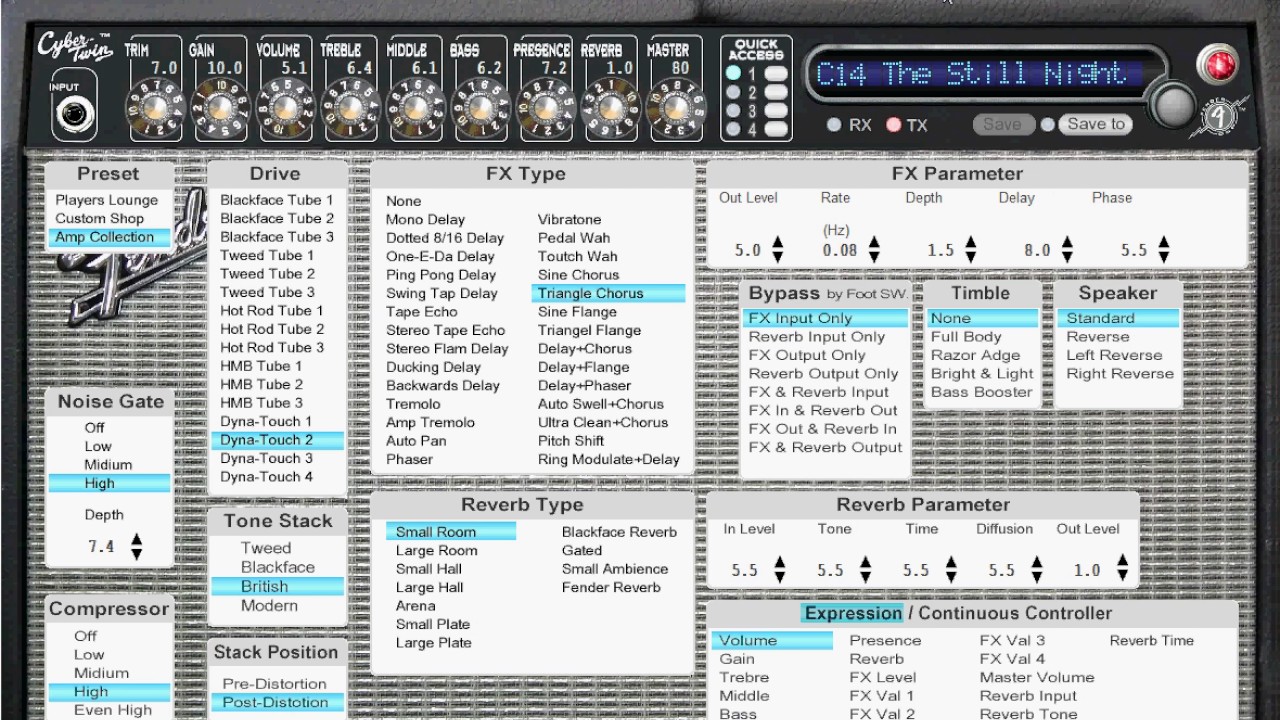
To accomplish this goal, end notched flexure (ENF) specimens are used in the experimental part (where the adhesive is submitted to pure shear loading) and two different models: a proposed damage model and existent cohesive zone model.īoth theoretical approaches are based in Griffith model, which establish the rate of relief of elastic potential energy stored in the system 𝒢, according to equation (1), as in.

The objective of this work is evaluating the critical energy relief rate 𝒢 IIC of the structural adhesives in mode II.
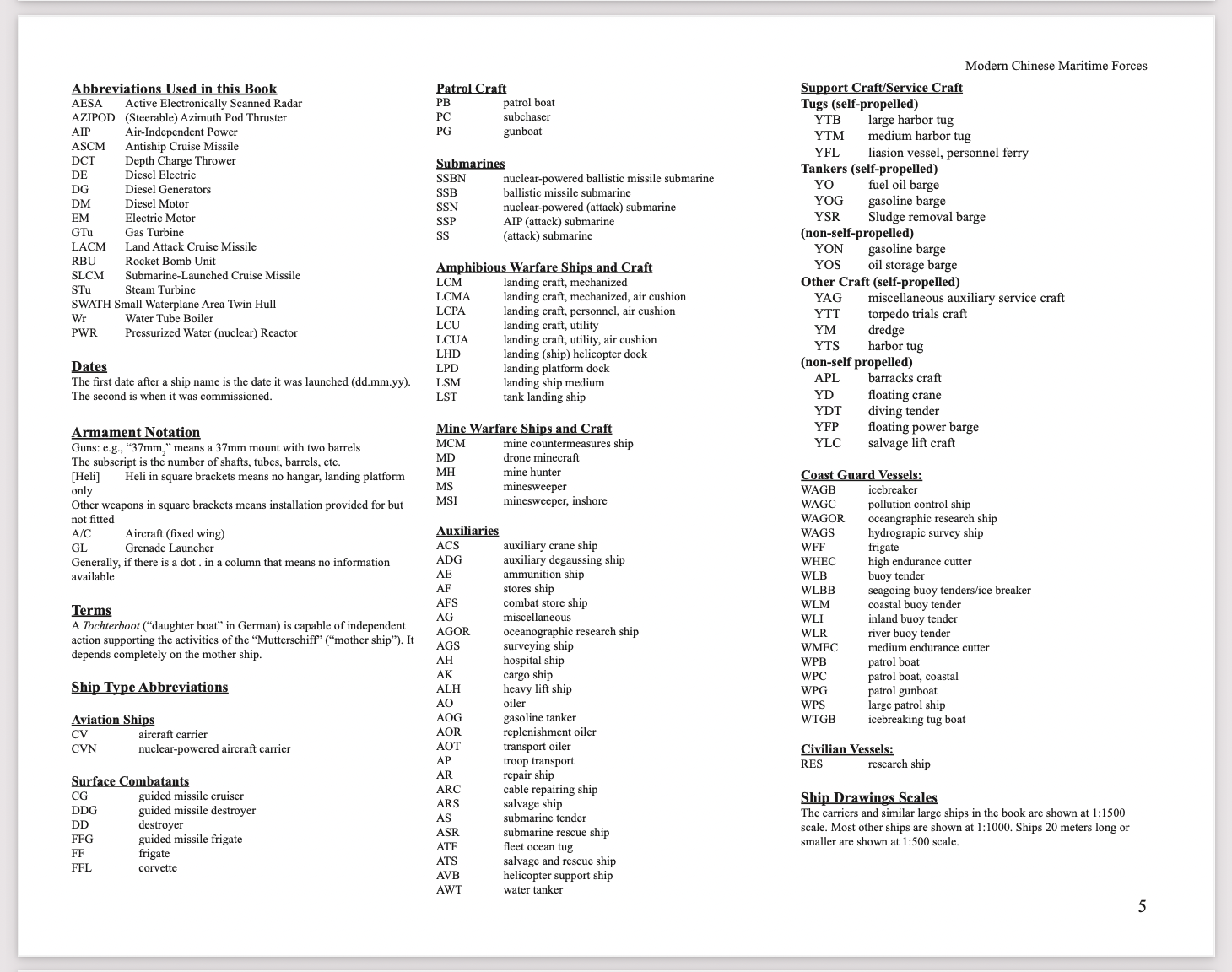
One typical example of the use of structural adhesives can be found in repair of pipelines with loss of thickness caused by corrosion. In fact, the adhesive bonding can substitute traditional joints as rivets and screws, with the clear advantage of diminishing the stress concentration effects. The actual development of high mechanical resistance adhesives finds a significant place in industrial applications. Structural adhesive joints are characterized by their simplicity and efficiency of use.
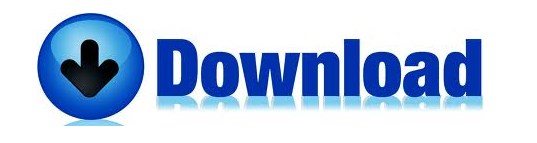